22 May Informe SOLDAMAN: Lo que tenemos que saber del acero inoxidable
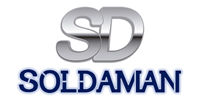
ARTÍCULO TÉCNICO
Lo que tenemos que saber del acero inoxidable
La necesidad de protegernos de los peligros fatales asociados a elementos corrosivos y a sólidos corroídos, nos llevó al empleo de útiles sanos, que habrían de ser fiables, de fácil construcción y limpieza, así como de costos asumibles; y, por lo tanto, al uso generalizado de este material.
Se nos introduce diariamente en la boca acompañando a los comestibles que nos nutren; llega a tocar de forma precisa y segura nuestros órganos vitales en las intervenciones quirúrgicas; también tiene contacto íntimo con los alimentos y las medicinas en su elaboración; se ocupa del tratamiento de residuos y productos tóxicos; está presente en la generación de energía, en el transporte, en la industria aeroespacial, en el mobiliario urbano, y en todos aquellos elementos que pueden considerarse de la máxima exigencia.
Se trata del acero inoxidable (nombre inadecuado, porque los únicos metales que no reaccionan con el oxígeno son el oro y el platino), y su misión distintiva consiste en ser tan resistente a la corrosión como sea posible.
Sus orígenes se encuentran entre finales del siglo XVIII y principios del XIX en Francia y Gran Bretaña, cuando distintos científicos fueron descubriendo progresivamente el cromo, uno; la resistencia que los “aceros al cromo” ofrecían a los agentes oxidantes, otros; el comportamiento positivo de las aleaciones de hierro y cromo contra el ataque de algunos ácidos, un tercero… Aunque la primera patente se produjo en el Reino Unido en 1861 por el Acero al Cr, fue en 1912 cuando se registró la actual y popular aleación de acero inoxidable austenítico 18/8 o AISI304. Desde entonces, nos acompaña como uno de los metales más eficaces y fiables de nuestro día a día.
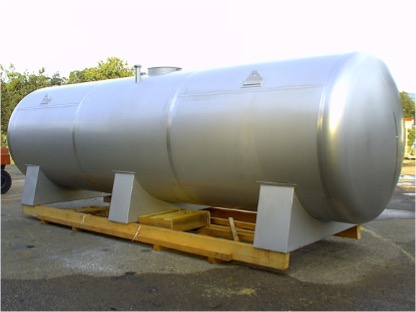
Ya se ha apuntado que lo que conocemos como acero inoxidable es una aleación de acero al carbono que se ha enriquecido con cromo; exactamente con un mínimo del 10,5%. Dependiendo de sus posibles estructuras cristalinas esta familia de aceros, muy ampliada en la actualidad, se divide en austeníticos, ferríticos, martensíticos y dúplex/superdúplex; según los contenidos del ya citado cromo, del níquel, del carbono… Y sus características mecánicas y comportamiento ante la corrosión también serán diferentes.
La característica principal de todos ellos es que el fundamental elemento de aleación, el cromo, se combina de forma autónoma con el oxígeno del aire y forma una película invisible de óxido de cromo, lo que damos en llamar capa pasiva, que protege al conjunto aislándolo de las condiciones del ambiente y, por lo tanto, de los agentes corrosivos que este pudiera contener.
Una vez presentados el porqué y el paraqué básicos del acero inoxidable hemos de ocuparnos de prevenir una cierta cantidad de problemas de corrosión sobrevenidos en este metal.
Cuando recibimos el material en nuestra planta, procedente del fabricante, este se encuentra, con seguridad, en perfectas condiciones, manteniendo sus propiedades características. Claro que las chapas, los tubos, las barras, han llegado al taller para sufrir alguna transformación: doblado, punzonado, corte, soldadura, mecanizado… Y todas esas operaciones, además de la manipulación física habitual, producen la rotura inmediata de la frágil capa pasiva que dota al acero de las ya descritas condiciones de “inoxidabilidad” (la película de protección tiene un espesor de 0,06-0,08 µm -un cabello humano es unas 2000 veces mayor, midiendo normalmente 70-170 µm de diámetro).
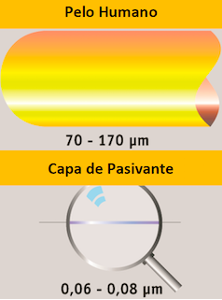
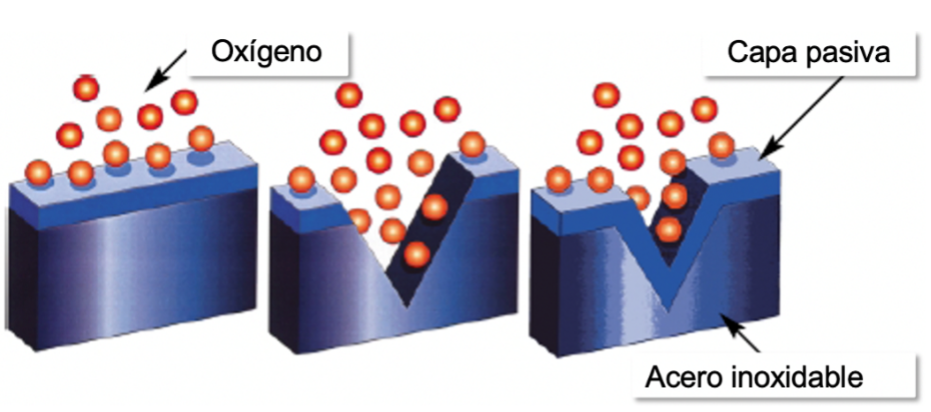
Esto no debería ser un gran problema en sí mismo, puesto que ya hemos dicho que el cromo del material y el oxígeno del aire reaccionarán y reconstruirán nuevamente la película protectora. En efecto, así es, pero, aun aceptando que el proceso de regeneración tendrá una duración de 48 horas, y que durante ese tiempo el proceso seguramente estará fuera de control, ello solo ocurrirá si no hay nada que lo impida. Y esto es importante, porque elementos ajenos como polvo, suciedad de cualquier tipo, partículas de hierro, marcas por calentamiento o desbaste, manchas de óxido, marcas de electrodos, salpicaduras de la soldadura, manchas de decapantes, aceites y grasas, defectos de soldadura, marcas de tiza, rotuladores… o incluso una huella dactilar, entorpecerán el proceso impidiendo el contacto directo, y haciendo imposible la formación de ese óxido de cromo protector. Y el inoxidable, tan pronto como se exponga… se corroerá.
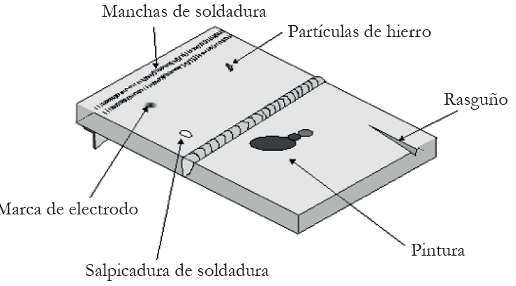
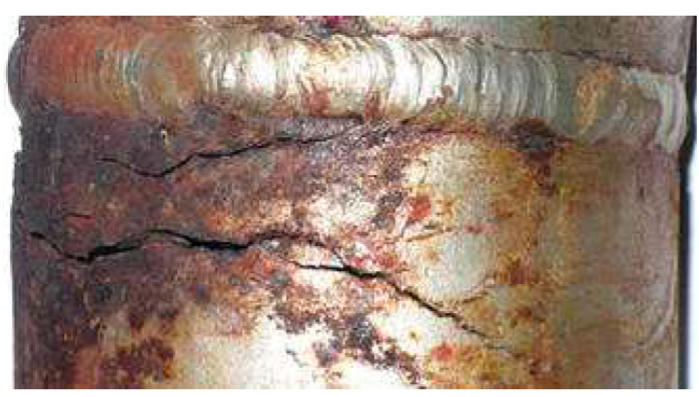
Si hasta aquí ha llegado la descripción del problema, a partir de este punto mostramos la solución fiable y segura que garantice la óptima puesta en servicio de las piezas o equipos. Es esta:
- DESENGRASADO químico del material, para eliminar las sustancias orgánicas que impedirían la actuación eficaz del decapante posterior.
- DECAPADO químico para la limpieza completa del metal; de esta operación el material sale vulnerable, y totalmente expuesto a cualquier agente externo, por la desaparición de la capa pasiva.
- PASIVADO mediante la aplicación de un producto que propicie la creación de la película protectora de forma muy acelerada (en minutos).
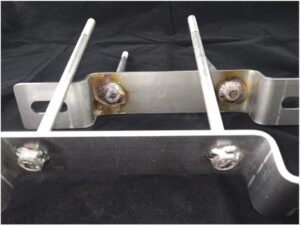
Si se ha realizado correctamente, el proceso recuperará la “inoxidabilidad” del acero. Naturalmente la operación de decapado puede sustituirse por un mecanizado, aunque habríamos de mantener el desengrasado (en este caso sería posterior porque tendrían que eliminarse los restos de lubricante) y el pasivado final.
Este trabajo se puede realizar por inmersión, sumergiendo las piezas alternativamente en los líquidos adecuados, o por proyección, pulverizándolos sobre aquellas, cuando se trate de equipos voluminosos o fijos.
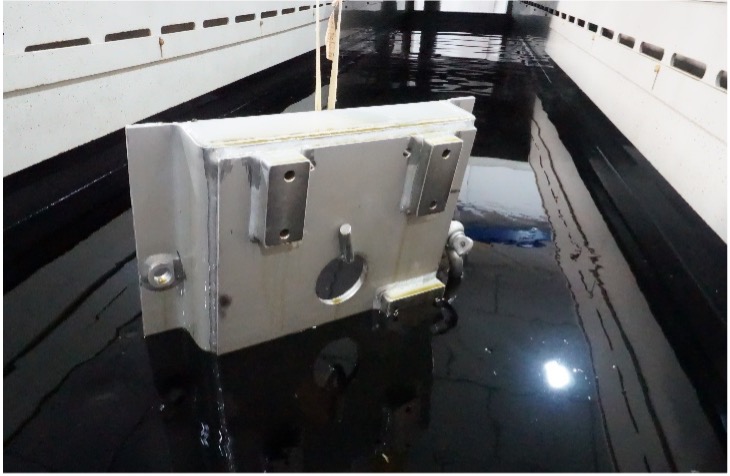
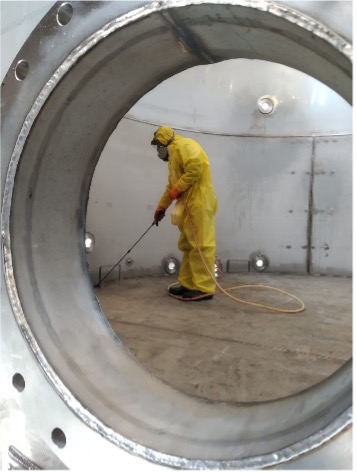
Los productos empleados para la realización de estos trabajos han sido tradicionalmente (todavía lo son) ácidos fuertes que exigen su tratamiento como residuo tóxico. Los desarrollos actuales más evolucionados, sin embargo, y sin que podamos dar por definitivamente resuelto el problema, nos ofrecen soluciones químicas biodegradables y/o menos agresivas para el medio ambiente; también su manejo es más seguro para el operario. En efecto, el desengrasado y el pasivado se pueden hoy realizar con compuestos que no son contaminantes; mientras que el decapado se efectúa con productos que, ofreciendo el mismo resultado, ven reducida muy notablemente la irritabilidad de los vapores que se producen a la hora de aplicarlos.
Las normativas que orientan y marcan las pautas son, entre otras, la ASTM A380, la ASTM A967, la AMS2700C, la UNE EN 2516, la ASME BPE…
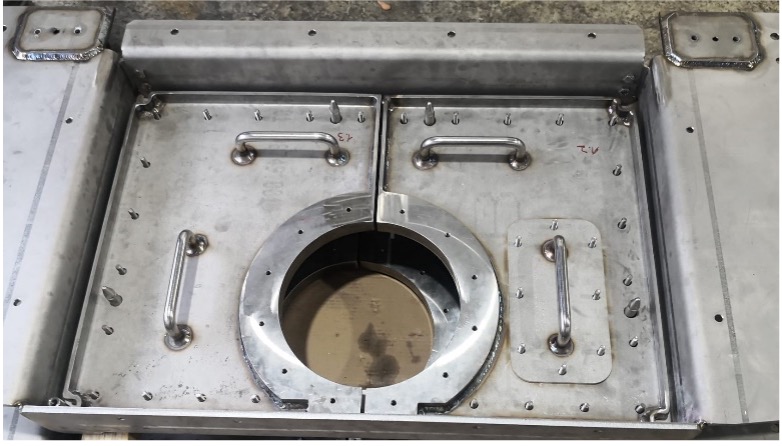
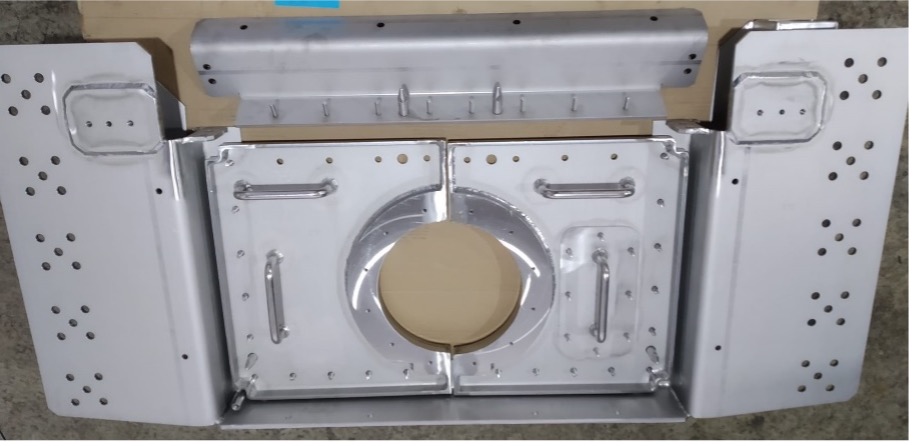
En definitiva, el acero inoxidable garantizará su comportamiento originalmente resistente a la corrosión, siempre que se cumpla adecuadamente el proceso anterior. Si así se hace, este mantendrá su “inoxidablidad” allí donde sea necesaria, en todo su universo de aplicaciones, que va desde lo más íntimo de nuestro organismo hasta el más expuesto lugar del espacio infinito.